Concrete is one of the most widely used construction materials in the world, with many key advantages such as formability and durability[i]. Concrete also has high compressive strength, which is defined as the maximum compressive load a body can bear prior to failure. However, concrete is actually quite weak in tensile strength, meaning that concrete is not an ideal material if the structure is subjected to tension.
Due to this inherent weakness in concrete, another material is needed to strengthen the tensile strength and avoid unacceptable cracking and even failure. Steal reinforcing bars can be added to resist the tension a load could cause for the structure. However, with the added material, new problems arise, such as corrosion of the steel rebar, which can cause a new set of issues for a construction project.
Overall, corrosion is a natural and costly process of destruction, just like earthquakes, floods and the occasional destruction caused by a tornado.[ii] However, unlike the onslaught of a tornado or earthquake, corrosion is silent and can be prevented, or at least controlled. The ASTM (American Society for Testing and Materials) defines corrosion as: ‘the chemical or electrochemical reaction between a material and its environments that produces a deterioration of the material’[iii]. In the same vein, corrosion is a naturally occurring process and all natural processes tend toward the lowest possible energy states.
Corrosion of reinforcing steel in concrete is a global problem, deteriorating structures at an extremely high rate. The issue makes up for more than 80 percent of all damage to reinforced concrete structures, continuing to rack up repair costs for countries[iv]. A 2011 report in the Journal of Climatic Change noted that the annual cost of corrosion worldwide is estimated to exceed $1.8 trillion[v]. With repair to steel in concrete climbing, sustainability measures cannot be feasibly met.
Corrosion
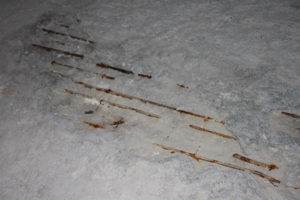
When the signs of damage became visible,
the extent of corrosion on the
reinforcement steel generally has
already reached an advanced stage.
There are three essential components necessary for corrosion in reinforced concrete: steel, water, and oxygen. Eliminating any one of these will prevent the chemical reaction and damage incurred due to corrosion. This is why there is no corrosion in dry concrete and also why concrete fully submerged in water has limited corrosion.
Overall, concrete is a great host for rebar. Due to the high-alkalinity of concrete, the steel reinforcing bars are passivated by an iron oxide film (Fe2O3) that provides a protective layer to the steel. In this state, concrete normally provides reinforcing steel with corrosion protection. However, while hardening, concrete develops minute pores which become a potential source for the ingress of corrosive agents into the concrete. These corrosive agents, entering into the concrete through the voids, leads to the passive protection layer breaking down around the concrete. Without the passive iron oxide film protecting the steel, corrosion is able to commence at a much higher rate.
The passive layer can deteriorate over time due to atmospheric carbon dioxide (CO2), which, through a process called carbonation, lowers the pH of the concrete until the passive layer becomes unstable. The passive layer can also be rapidly broken down by aggressive chemicals, such as chloride, that are present in coastal environments or used in de-icing chemicals. Once the passive layer is compromised, steel reinforcement corrodes when moisture and oxygen are present at the steel’s surface.
The climatic conditions of an area have a great influence on the corrosion rate. In extreme climatic conditions in coastal regions, the rate of corrosion will be high. For example, the Gulf Coast has an extremely aggressive environment, characterized by high ambient temperature and humidity conditions, severe ground salinity with high levels of chlorides, and sulfates in the groundwater. Other factors accelerating the rate of corrosion are the poor quality of construction materials, particularly the aggregates, and the presence of high concentrations of sulfate salts in the service environment.
Negative effects
Steel reinforcement is needed for concrete
to increase its tensile strength.
As mentioned earlier, corrosion is a natural process. Steel is a manufactured material produced from iron oxide or iron ore. Unfortunately, the energy added in the refining process also contributes to its instability. When a suitable environment or condition arises, steel releases energy and converts itself into iron oxide. This natural state of iron is a thermodynamically stable material.
The steel rebar used in concrete strengthens the structure by providing a solid tensile strength concrete normally lacks. When the steel begins to rust and produce pits or holes in its surface, a reduced strength capacity is seen, which negatively affects the structure’s viability.
Corrosion begins to affect a concrete structure’s integrity when the products of corrosion (i.e. rust) occupy a greater overall volume than the original steel. This expansion then creates tensile stresses in the concrete that cause the concrete to stain, crack, and spall. By the time the signs of damage become visible externally, as in on the outside of the concrete structure, the extent of the corrosion of reinforcement steel has reached an advanced stage. At this point, regardless of where the site is located, the rehabilitation costs will be expensive, and the repair process complicated. [vi]
There are multiple steps on the way to corrosion, beginning with aggressive elements, such as chloride ions or carbon dioxide being present in the surrounding medium and penetrating the concrete. The second stage after ‘initiation’ is ‘propagation,’ which happens when these aggressive bodies are in rather high concentrations at the reinforcement level. The passive layer is gone and corrosion damages the structure at a much higher rate. [vii]
Subsequent to corrosion, cracks appear on the external concrete surface. Cracks are a direct path for corrosive agents to penetrate and reach the steel. These cracks will further progress and develop into spalls to the point where the functional service life is reached, prematurely. Therefore, water must be kept from penetrating the reinforced concrete and diverted away from attacking the steel rebar within.
Traditional methods to prevent corrosion
There are some methods for controlling the corrosion of reinforced concrete. An effective corrosion control system should extend the time to corrosion initiation or, reduce the corrosion rate of embedded steel, or do both.
Some of the traditional measures used to combat the corrosion of reinforced concrete are:
- Cathodic protection;
- Corrosion inhibitor admixtures; and
- Anti-corrosion coating.
When the steel begins to rust and
produce pits or holes in
its surface, strength is reduced.
Unfortunately, these traditional methods meant for tackling concrete corrosion have proven to be less effective than desired considering the current state of deteriorating infrastructure. Thick or dense concrete cover over reinforcing steel will help, but still leaves the concrete vulnerable to cracking and a whole new set of issues. Corrosion inhibitors provide only temporary protection. Cathodic protection is expensive and has its own downsides, and repair procedures often have short service lives and may be continuously reinstalled.
The constant repair of reinforced concrete infrastructure results in high lifecycle costs over the structure’s required service life. Overall, the shortfall of traditional corrosion preventative measures is they do not adequately prevent or counteract the development of corrosive conditions in the concrete.
As mentioned, water is one of the three required elements for corrosion to occur. Water also acts as a carrier for chloride ions, which is the leading cause of deterioration of the passive layer that would otherwise protect the rebar. Hence, the critical factor in the corrosion of steel reinforcement, as well as concrete deterioration all together, is the penetration of water and waterborne chlorides into concrete.
Therefore, the first line of defense against corrosion in reinforced concrete is to prevent the penetration of water. It is important to use concrete with low permeability and to use an appropriate amount of concrete cover for the application.
Waterproofing strategies
Concrete is a hard material with a network of openings such as capillaries, pores, cracks, and micro-cracks. Water can pass through unprotected concrete, acting as a carrier for aggressive chemicals like chloride, which will corrode reinforced steel rebar.
The membrane was damaged
in multiple areas after the
initial placement by construction
materials used to complete the
structure.
With the exception of mechanical damage, all the adverse influence on durability in concrete involves the transport of fluids through the concrete.[viii] Water permeability determines the rate of deterioration, which means if the concrete is protected against the ingress of water, the durability of the structure will increase and in the end the service life. As a result, reducing the permeability of the concrete is key. Unfortunately, as with the protection of reinforced concrete, traditional measures are not living up to expectations.
Surface-applied membranes or sheet membranes are one option to consider. This membrane forms a barrier against water penetration on the outside of the concrete. Another option is a fluid-applied membrane. In the same manner as a sheet membrane, the fluid-applied membrane forms a barrier on the surface of the concrete to stop water penetration.
In both circumstances, the traditional waterproofing system is providing a barrier to the concrete. However, surface-applied waterproofing membranes have limitations and are at risk to puncture damage and failure. Moving away from the tradition, success has been obtained by replacing the need for an external membrane and replacing it with an internal membrane, thereby making the concrete the waterproofing barrier.
Integral crystalline waterproofing admixture
Millions of needles like crystals grow to stem
the flow of water within reinforced concrete.
A permeability-reducing admixture suitable for hydrostatic conditions (PRAH) such as integral crystalline waterproofing (ICW) admixture is included with the concrete mix at batching or directly to the ready-mix truck. Instead of adding the installation of a sheet membrane or the application of a fluid membrane, an ICW eliminates that need by becoming part of the concrete mixture. The ICW admixture is effective in reducing concrete’s permeability without costly materials, labor or time required to install the external methods.
The features of an ICW admixture provide many unique benefits to concrete enhancing the durability for the properties of concrete that have historically resulted in poor durability. Through the use of crystalline technology, the ICW admixture reduces the penetration of water and water-borne chemicals through three primary mechanisms:
- crystallization and lowering the permeability of the concrete;
- reducing the size and quantity of cracks in the concrete; and
- self-sealing cracks and micro-cracks that form later in the life of a structure.
The effects of ICW’s have been seen not only in numerous projects worldwide but also in a unique long term study that has been performed by the University of Hawaii.
Conclusion
ICW can control the corrosion in reinforced concrete by impeding the development of corrosive conditions caused by the penetration of moisture. The result is a structure with increased durability, a longer lifespan and lower maintenance costs over the structure’s service life – all essentials in today’s sustainable building practices.
[i] World Business Council for Sustainable Development’s (WBCSD’s) “The Cement Sustainability Initiative–Recycling Concrete” at www.wbcsdcement.org.
[ii] Zaki Ahmad’s ‘Principles of Corrosion Engineering and Corrosion Control’, 2006
[iii] http://www.astm.org/SNEWS/ND_2009/j01_nd09.html
[iv] Sam Mathew’s ‘Concrete Corrosion, Methods to Control this Perennial Problem in the Middle East’, 2006
[v] Impact of climate change on corrosion and damage to concrete infrastructure in Australia 2011
[vi] For more see Sam Mathew’s ‘Concrete Corrosion, Methods to Control this Perennial Problem in the Middle East’, 2006
[vii] Rasheeduzzafar and Kurdi, A, “Effect of Hot Weather Conditions on the Microcracking and Corrosion Cracking Potential of Reinforced Concrete,” Durable Concrete in Hot Climates, Cameron MacInnis Ed, SP-139 (1), American Concrete Institute, 1993.
[viii] Adam M. Neville’s ‘Properties of Concrete’. 1996